May 4, 2006
Kinko's opened up in Japan some years back, and has both increased my options on hanshita preparation and reduced my costs. Mostly it's because they always have the highest quality copy machines on hand, and these are always in good condition. Are you concerned that I am using too much high-tech in this project? Aren't I supposed to be using 'pretty much just the old Edo-era techniques' for my work?
I have drawn my own line on this matter, and this step is where it lies. I will use whatever technology necessary to get the image manipulated into carveable form, but once that's done and ready to be applied to the blocks, from then on the only divergence from 'how it was done in the old days' will be those cases where original materials are no longer available to any of us (pigments, etc.)
So here we are in Kinko's. I 'rented' one of their computers, and printed my tracing out onto glossy A2 size paper. I then took that sheet over to their bank of copy machines, and took 20 copies of it on a special paper that I brought with me, watching like a hawk to make sure the paper came through the machine smoothly and without bunching or twisting.
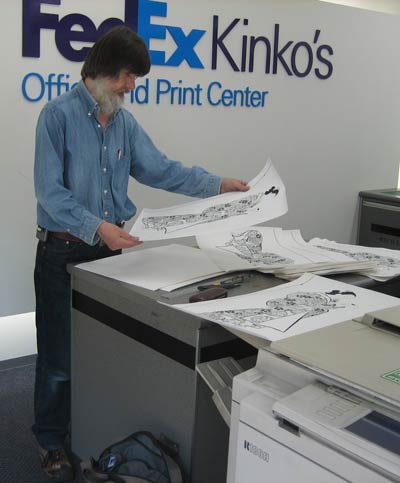
This special paper is made of two layers of washi: a cheap 'base' sheet with a layer of very thin paper laminated on top of it. The hanshita on the block of course has to be very thin, to allow the image to be clearly visible for cutting, but such thin paper will not go through these machines. Laminated like this, there is no problem at all in getting the image printed onto the thin paper. For most of my printmaking in recent years, I have made up such paper by myself, using a spray adhesive to create the laminate, but for the large sheets necessary for this project, I bought a commercial version.
Here's what they look like; back at home I have trimmed the two registration marks just up to the printed line ...
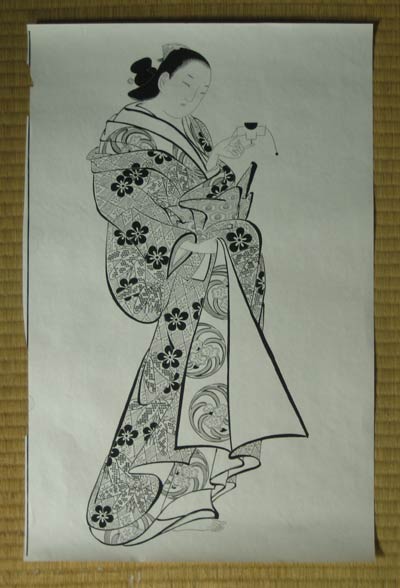
... and then used a bit of nail polish to stiffen the paper at those two points.

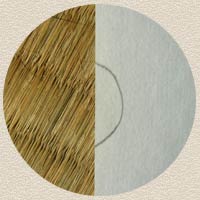
Then begins the long process of marking up the sheets to show just what part of the wood needs to remain, and what is to be cut away. I have been thinking about this off and on for the past couple of months, especially while I was doing the tracing, and think that I have a basically sound iro-wake (colour separation) worked out.
Some parts are easy - the main red kimono area is pretty obvious - but there are many places where the decision making is not so clear, usually in those places where the opaque pigment in the original obliterated some of the lines. Anyway, here are a couple of them ...


I took 20 copies from the master at Kinko's, and that will be enough to get me going, but there will definitely be more than that needed for this print before we're done. But there are many complexities still to come, so at this point, I'll just get started; once the major group of 'core' blocks is ready, I'll do some test printing, to sort out some of the unresolved issues, and will then prepare more as seems necessary.
Here's the starting batch of colour separations ...
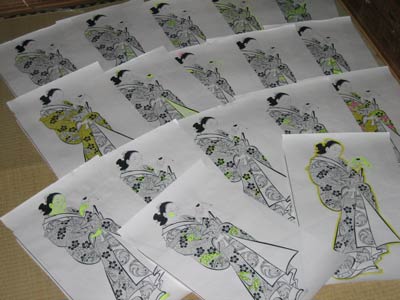
Next step - getting them pasted in place on the wood!
